Auto Assign use cases
Use Case: Staffing for seasonal changes in hospitality
Scenario
A hotel chain experiences seasonal demand fluctuations, with higher occupancy rates during summer and holidays and lower rates during off-seasons. The optimal number of front desk agents, housekeeping staff, and kitchen crew must align with guest bookings.
Solution
- Define Optimal Headcount Variables for each department (e.g., front desk, housekeeping, kitchen) based on forecasted guest arrivals and room occupancy.
- Apply Static Rules to ensure critical roles, such as one front desk agent per shift, are always covered.
- Use Static Rules for housekeepers, scaling staff based on the number of occupied rooms, allowing for flexibility during peak and off-peak seasons.
Outcome
The hotel operates efficiently with the right number of staff to deliver excellent guest experiences, avoiding both overstaffing and understaffing.
Use Case: Managing headcount in a manufacturing plant
Scenario
A manufacturing plant produces goods based on demand forecasts. As production ramps up or slows down, the number of machine operators, quality inspectors, and assembly line workers need to align with the production schedule.
Solution
- Create Optimal Headcount Variables for each role tied to production forecasts, such as units produced per hour.
- Use Min/Max Rules to set minimum staffing levels for critical roles like machine operators to ensure continuous production, while limiting maximum staffing for roles with physical space constraints on the assembly line.
- Incorporate Labor Standards with Linear Rules to calculate staff needs based on the number of units forecasted per hour.
Outcome
The plant maintains high production efficiency, ensures product quality, and optimizes labor costs by adjusting staff levels in real-time to meet demand.
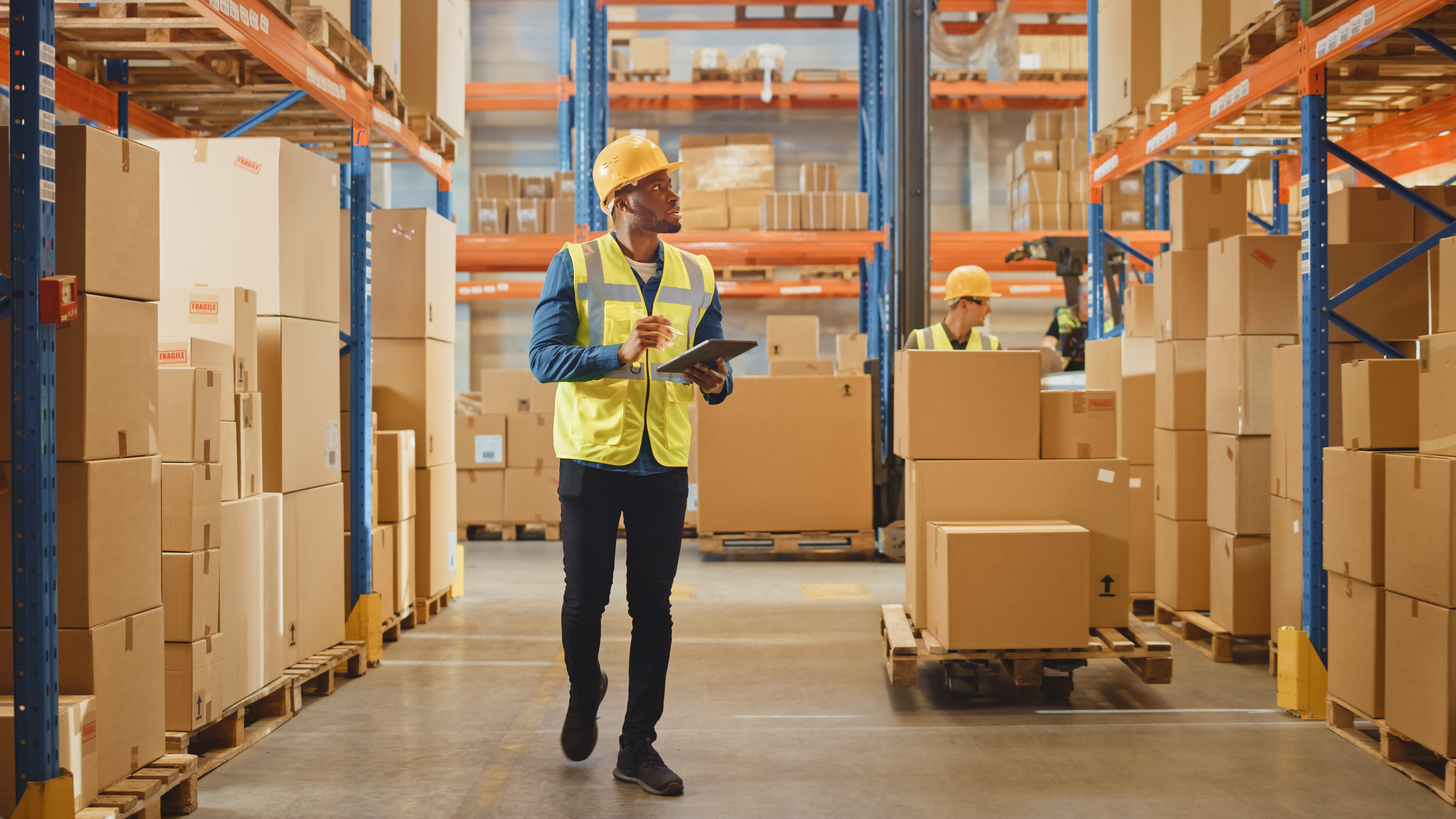
Additional information
In general, dynamic rules are used when increased forecast levels result in higher productivity. For example, when employees can handle tasks more efficiently as demand grows. On the other hand, linear rules are applied when increased forecasts don’t lead to higher productivity, such as when it takes the same amount of time to place a product on a shelf, regardless of demand.
It’s uncommon to combine both types of rules for the same role.
Dynamic rules are also often favored by less “mature” organizations—those that haven’t yet analyzed precise task times. For instance, instead of calculating the average time it takes for a barista to prepare a coffee, they may rely on general knowledge or experience. For example, they know that on a busy day (defined as 100+ visitors per hour), they’ll need three cashiers scheduled to prevent overwork and ensure reasonable queue lengths.